If you follow Heliogen, you’re likely familiar with the Capella project. Jointly funded by Woodside Energy and the US Department of Energy, the Capella project will be a first-of-its-kind 5-MWe concentrated solar power plant utilizing “Gen 3 Concentrating Solar Power (CSP)” technology. Our Gen 3 CSP system relies on solid particles to transfer and store thermal energy, unlike Gen 2 CSP systems which use molten salt. Capella will include three critical first-of-a-kind components: the particle receiver, a particle-to-supercritical carbon dioxide (sCO2) heat exchanger, and a sCO2 Brayton cycle power block. Each of these three components is going through a rigorous engineering, verification, and scale-up process to prepare for deployment.
In an important step toward the construction of Capella, Heliogen has recently achieved a critical milestone in the development of the first commercial-scale particle receiver. We validated several important design improvements necessary to hit all of Capella’s cost, performance, and reliability targets.
As the literal focal point of a CSP plant, the receiver is subject to harsh conditions. It will absorb sunlight that has been concentrated over a thousand times. The receiver will accept particles that are already quite hot – over 400 oC – and will heat them up to output anywhere from 670 oC to 900 oC. Lastly, the receiver needs to start up and shut down daily as the sun rises and sets. With those challenges in mind, Heliogen has been rigorous in our development and verification of the receiver. Most importantly, the technology is ready to scale up for Capella’s two receivers, which will be double the size and produce eight times the amount of thermal energy as the ones previously developed.
We completed the fabrication and delivery of the largest centrifugal particle receiver constructed worldwide. This receiver will operate up to 900 °C and at a thermal power level of 1 MW at peak operation, affirming Heliogen’s technology as a global leader in particle receivers. Most importantly, the technology is ready to scale up for Capella’s two receivers, which will be double the size and produce eight times the amount of thermal energy as the ones previously developed.
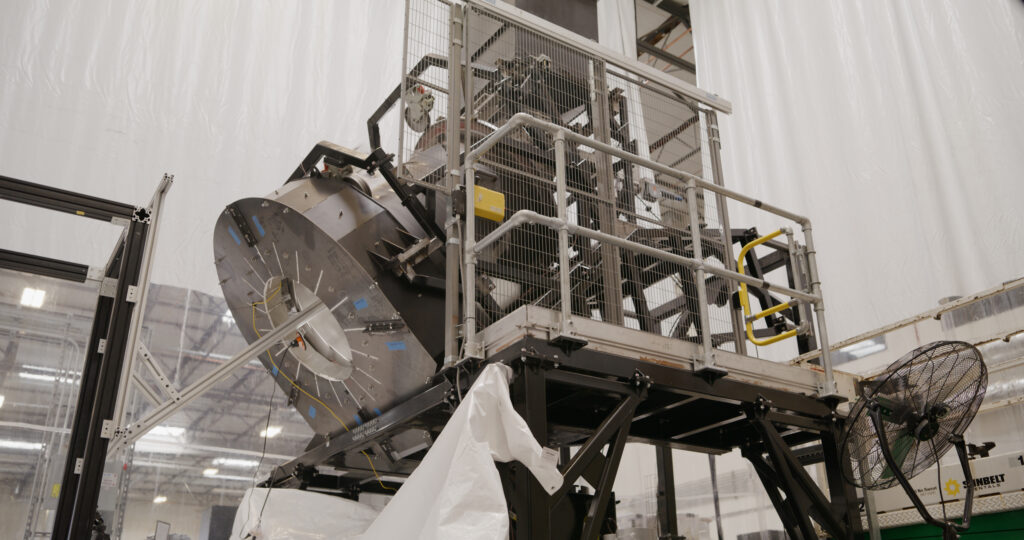
Based on lessons learned from deploying a pilot scale receiver, we knew we could improve on cost, ease of manufacturing, and efficiency. We made impactful design improvements that would allow for more accessible serviceability of components and better control the particle flow through the receiver. To allow for rigorous testing of these innovations, our team fabricated a smaller test receiver to validate they worked as intended. These successful test results have given us the insights we need to move straight into the detailed design and fabrication of the two full-scale receivers for Capella.
Upon completion, the Capella project will add to Heliogen’s portfolio of commercially ready technologies. Alongside the mature products we already offer for the industrial heat and large-scale power markets, the Gen3 CSP capabilities will broaden the space of potential applications to include variably sized power projects and improve the economics for customers.
With the open questions resolved on the centrifugal particle receiver’s design, we’re focusing our efforts on the particle-to-sCO2 heat exchanger and the sCO2 power block. These two components will implement industry-leading innovations of their own, and we look forward to sharing progress on those engineering efforts soon.